It’s versatile, light, carbon-capturing and may even make us feel better when we’re surrounded by it. Is timber the future of construction?
In Japan, the miyadaiku know an ancient type of carpentry that is used to build temples. They believe the characteristics of trees and the intentions of the miyadaiku should co-exist in harmony; they are as one.
It takes years for a miyadaiku to become a Toryo – master carpenter – if they ever get there. Only one in every 100 apprentices achieve such status.
The craft is guarded: knowledge is passed on orally – nothing is written down. Apprentices learn by watching and by doing. A Toryo restoring a pagoda in 2021 will find unity with the miyadaiku who built the structure in 800 AD. Even the tools, the axes and the spear planes, haven’t changed for centuries.
In 1934, this process allowed the Nishioka family to restore the world’s oldest wooden building, Hōryū-ji in Nara. Built in 708 AD, it took the family 51 years to dismantle the ancient beams and tiles, refurbish them and rebuild it all.
More than 1,400 years on from the construction of Hōryū-ji and timber is still the only sustainable building material the construction industry has widely available. Despite all the advances in technique and technology, the reinforced concrete and the super-strength steel, some believe that only wood can help to avert climate disaster.
Construction’s environmental footprint is huge. The sector creates 38 per cent of global energy-related CO2 emissions. Concrete production around the world is responsible for 9 per cent of industrial water use each year.
The global building stock is expected to double in area by 2060 – equivalent to adding a New York City each month for 40 years. So it’s time for the industry to take a long, hard look at itself in the reflection of a glass skyscraper.
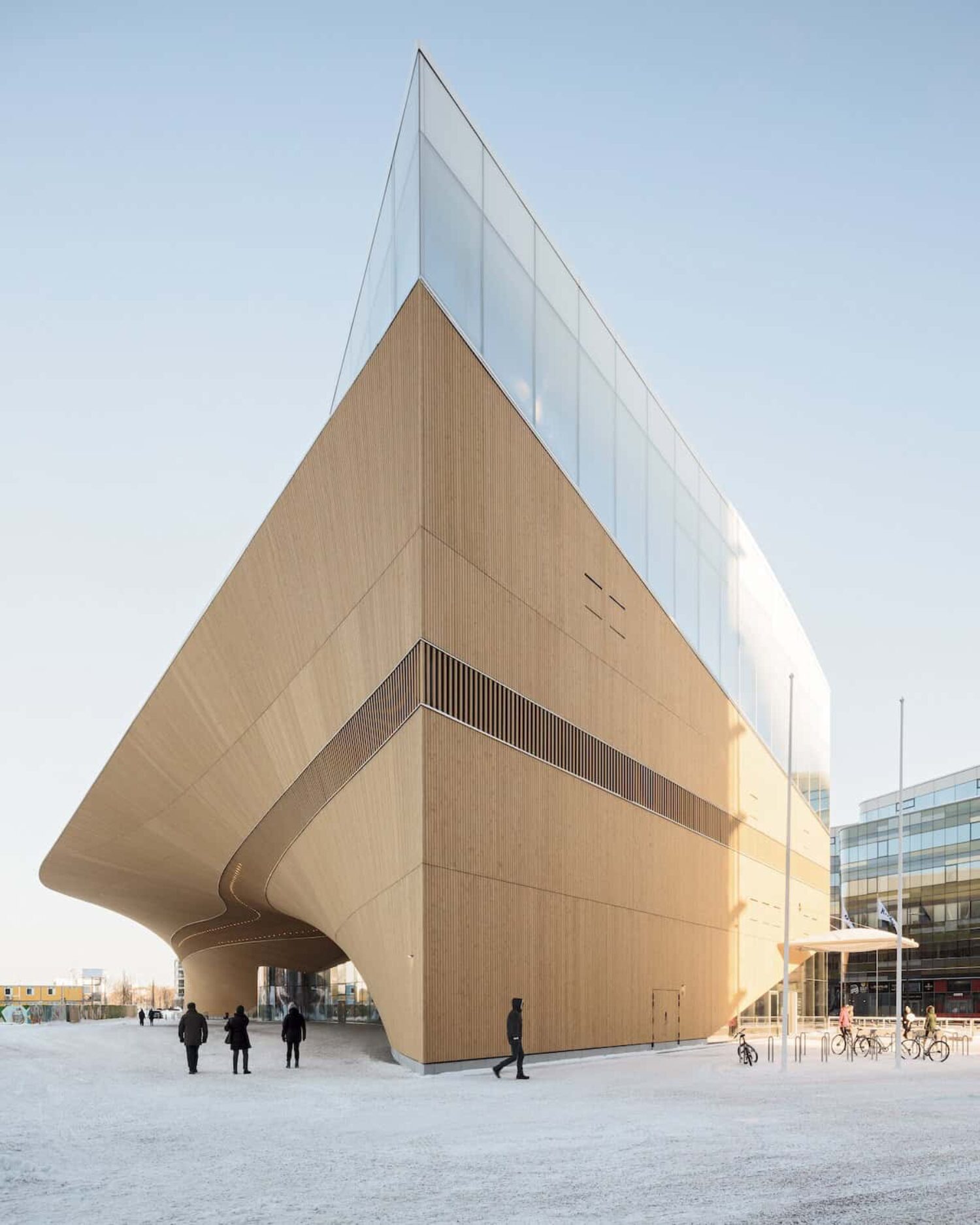
Out of the woods: timber features heavily in the Helsinki Central Library. Credit: Helsinki Central Library
“We believe buildings ought to do more to counteract their negative environmental consequence,” says Alysia Baldwin, an architect at global design practice Perkins&Will.
The firm has designed Earth Tower, a 40-storey building in Vancouver. When complete, it will be the world’s tallest hybrid wood tower. Its lateral stability will come from reinforced concrete elevator cores, but the floor slabs, walls and columns will be made from locally manufactured mass timber.
For the construction industry to reach net zero by 2050, direct building CO2 emissions need to drop by 50 per cent within a decade, estimates the International Energy Agency.
Wood needs to become the new standard in order to achieve that, says Gavin Tadman from the UK’s Structural Timber Association: “Timber is carbon negative from the cradle to the grave.”
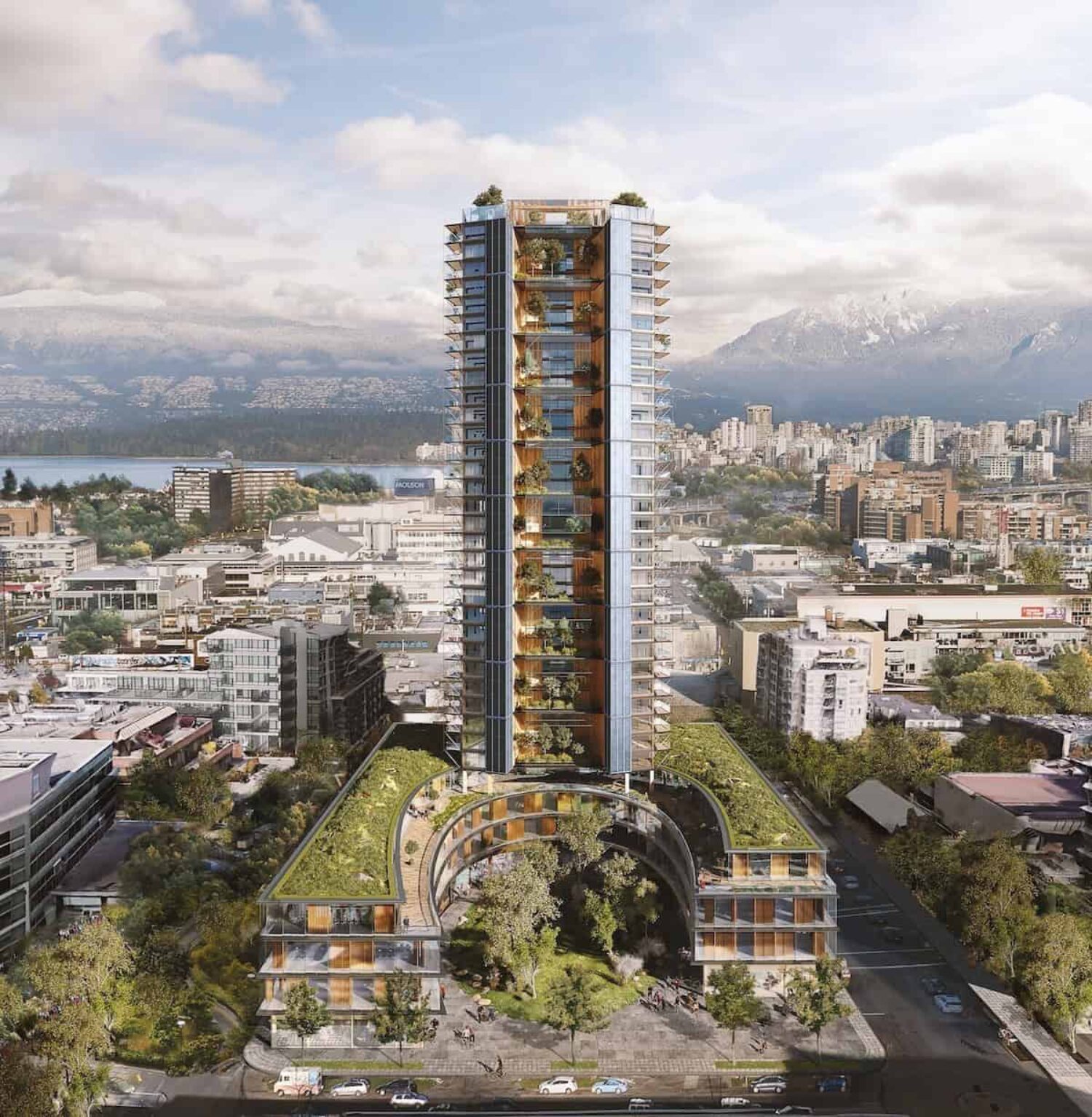
Canada’s Earth Tower is set to become the world’s tallest hybrid wood tower. Credit: Perkins&Will
Studies have shown that one cubic metre of cross-laminated timber (CLT) sequesters around one tonne of CO2. [CLT is layered wooden boards stacked together like Jenga pieces and glued for stability.] In comparison, concrete emits 150kg; steel emits 1.85 tonnes.
Researchers at the University of Washington found that a CLT building, from resource extraction through to construction, uses 26.5 per cent less energy than its concrete equivalent.
As a natural thermal insulator, timber performs 15 times better than concrete and 400 times better than steel, so less energy is required to heat a building.
An engineered wood frame is also around 30 per cent lighter than a concrete or steel equivalent, meaning less heavy machinery is required – in transportation as well as on-site – helping to speed up builds. For Dalston Works, a 10-storey, mixed-use development in London’s Hackney, that is built of CLT, 111 lorry loads were needed, compared to the 700 that would have been required for a concrete version of the building.
Timber is carbon negative from the cradle to the grave
When the world’s tallest timber building, Mjøstårnet, was erected in Brumunddal, Norway, it was built without external scaffolding, despite being 85.4m high.
Prefabricated elements were brought to the site, explains Rune Abrahamsen, CEO of Moelven Limtre, the firm that produced the glulam structures (timber laminations that are glued together and used for floor beams or trusses) used in the build. “The building was assembled four storeys at a time, with a total of five construction stages.” A crane helped to lift the largest components into place.
Timber buildings are getting lifts from elsewhere too. In 2018, the World Architecture Festival introduced a timber category as part of its annual awards, for example. Hours could be spent gawping at the entrants: the sweeping Finnish spruce hull of Helsinki Central Library, Oodi; the 45m-high hourglass lookout tower that spirals out of the forests near Copenhagen (main picture, above); or the sunlight shredding through the four timber pavilions of Pingelly Recreation and Cultural Centre in Western Australia (below).
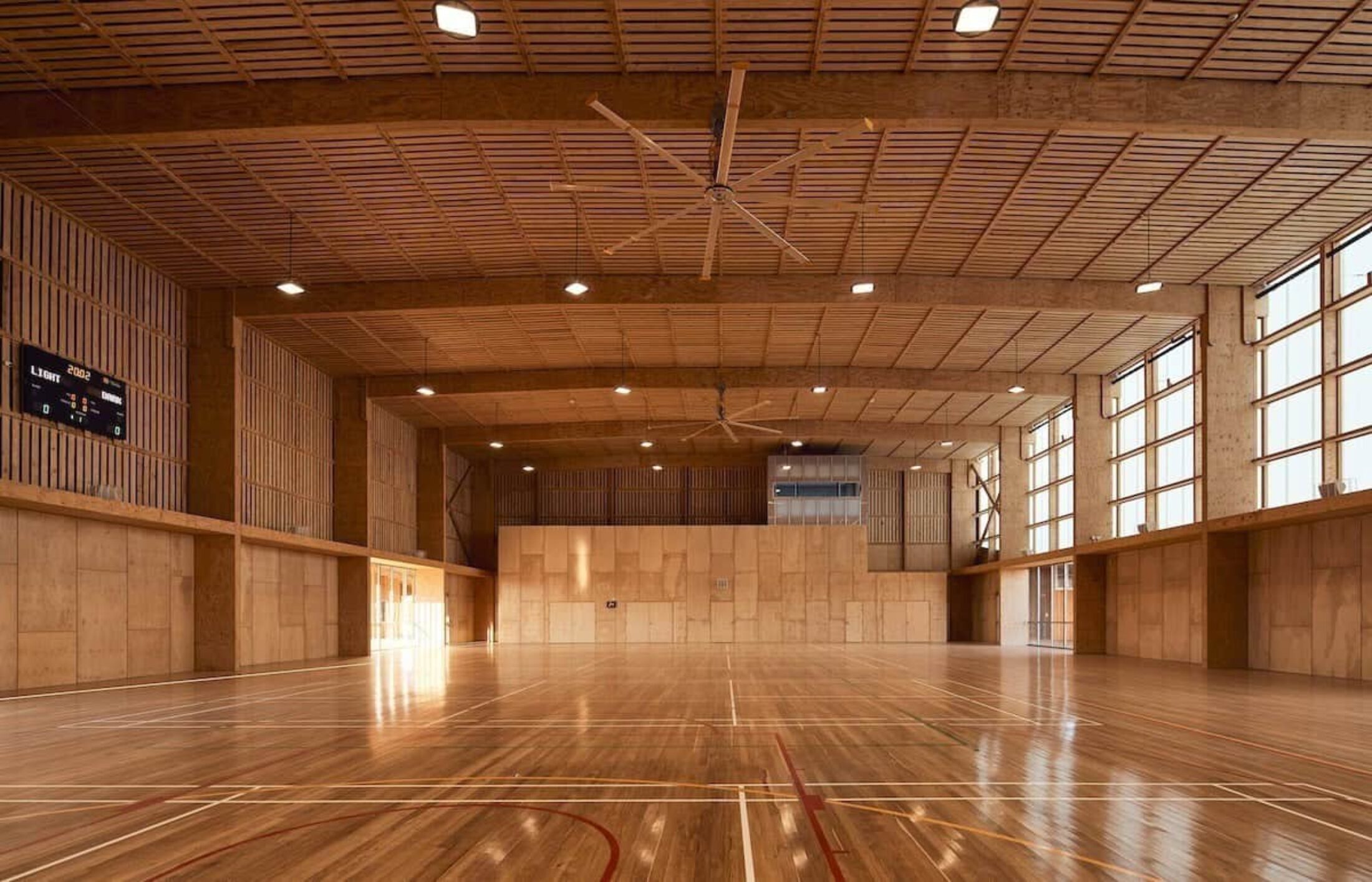
Australia’s Pingelly Recreation and Cultural Centre is made of locally grown Eucalyptus. Credit: Peter Bennetts
Building a human connection
Studies have shown that spending time in timber buildings can be calming. Research from Canada suggests that they have stress-reducing properties similar to being in nature.
A university in Finland even considered how people react to different woods. Glued laminated birch, old oak, oak log and grey oak were found to be “beautiful”, leading to positive emotions. Finely sawn spruce, laminate, oriented strand board (similar to plywood) and lacquered oak parquet were less popular.
Currently, the choice of wood is usually left to the architect, and many select native, locally sourced materials from sustainably managed forests.
“Spruce is primarily used throughout Mjøstårnet, both for glulam structures and CLT panels,” says Abrahamsen. Pine was chosen for the exterior, as it can be pressure-treated, making it stronger and resistant to termites.
Alysia Baldwin from Perkins&Will, often opts for Douglas fir because its “reddish colour provides beautiful warmth to a space when it is exposed”.
[Timber] is one of the most promising innovations in building
Mass timber, however, isn’t without its critics. The Sierra Club, a US environmental organisation, points out that the claimed benefits of swapping concrete or steel for wood is misleading when the impact of logging on forests is left out of the emissions equation.
It is calling for the establishment of a Forest Carbon Trust, to better protect woodland – in particular ‘primary forests’, those that are unlogged and that include old trees.
“Forests should be managed to optimise the amount of carbon they store regardless of ownership, and not for the quickest return on investment,” reads a Sierra Club report on the topic. Wherever logging takes place, climate- friendlier forests are a must, is the report’s “inescapable conclusion”.
The age of timber
“Timber is the new concrete,” said Alex de Rijke, director of London-based firm dRMM Architects, which has pioneered the use of wood in construction, speaking in 2015. “The 17th century was the age of stone. The 18th century was the peak of brick. The 19th century was the era of iron. The 20th century was the century of concrete. The 21st century will be the time for timber.”
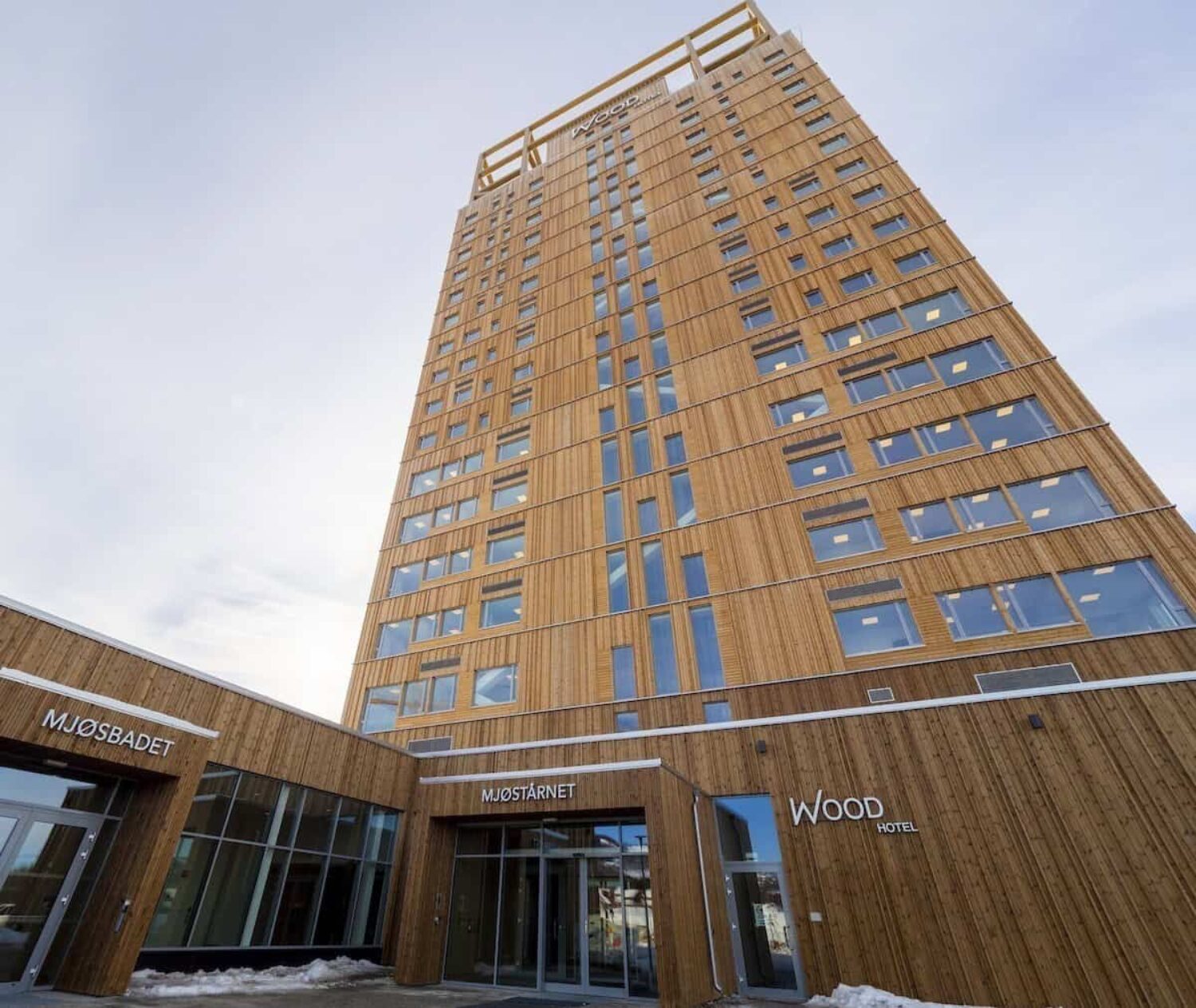
At 85.5m high, Mjøstårnet in Norway is the tallest timber building in the world. Credit: Moelven
Six years later, de Rijke’s prediction appears to be coming true. The US’s International Building Code is expected to allow timber structures up to 18 storeys high from this year, while any new buildings for the 2024 Paris Olympics below eight storeys must be made entirely from wood. Across France, there are plans for all new public buildings to use at least 50 per cent timber in their construction.
The chief perception that still needs felling? Fire safety. Following the Grenfell Tower disaster in London in 2017, the UK government banned timber, and other combustible materials, from the exterior of residential buildings that are more than 18m high. It is now proposing both to continue and extend the ban.
Architecture critic Rowan Moore recently wrote of the decision in the UK press: “Better, you will probably think, to be safe than sorry. But there’s a cost to this caution, which is that it will impede one of the most promising recent innovations in building.”
Organisations including the Architects! Climate Action Network and the Royal Institute of British Architects are urging the government to reconsider. Part of the problem is that the legislation doesn’t adequately distinguish between the cladding, or outer skin of a building, and its structure, Moore points out.
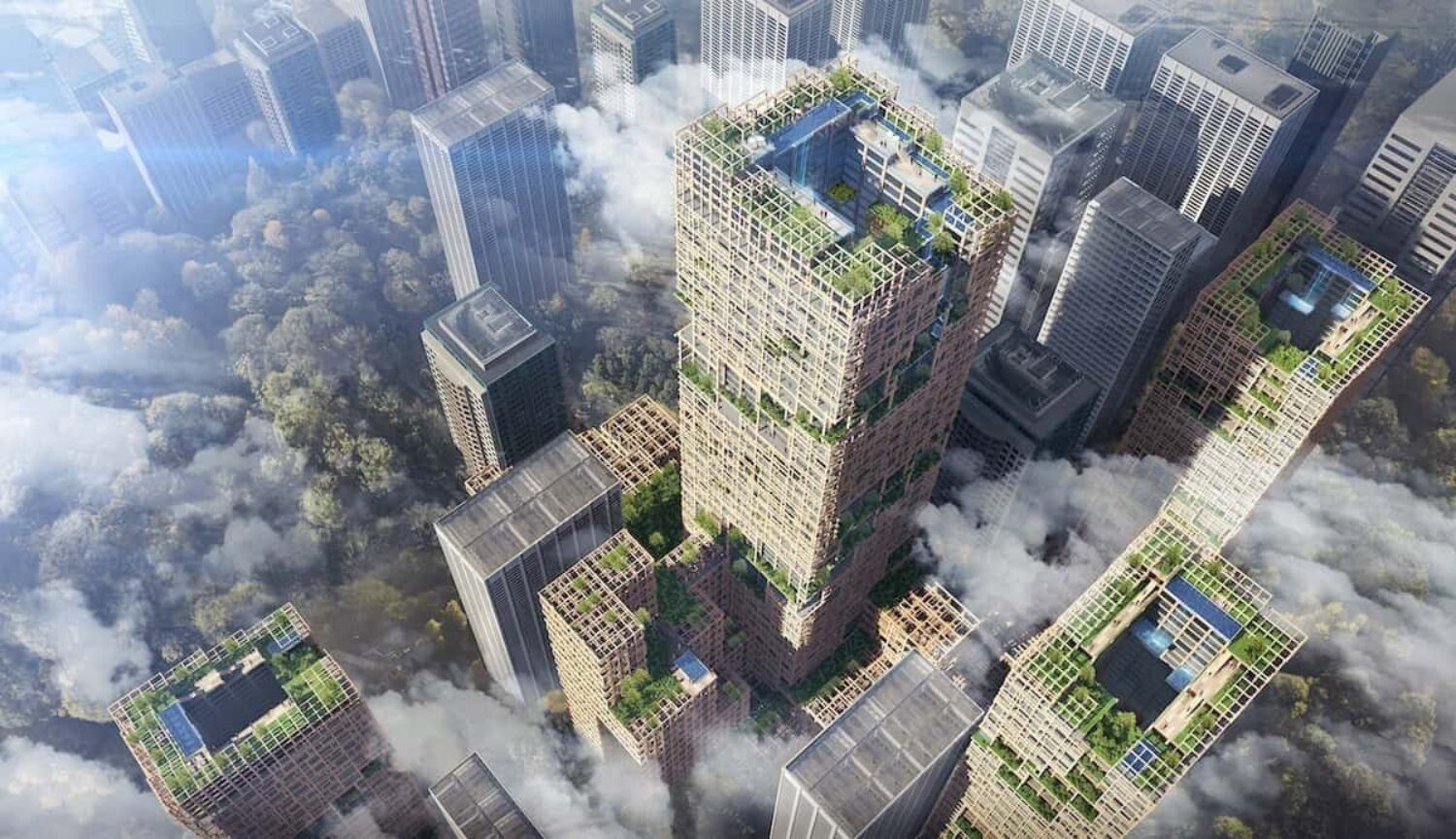
Renderings of proposed timber skyscraper in Tokyo. Credit: Sumitomo Forestry
Tests in the US have shown that plaster-coated CLT lasts nearly 60 minutes longer in a fire than regulations require. Firefighters often consider wood-based fires to be more predictable: timber holds its structure for longer compared to metal, and doesn’t give off toxic chemicals.
While caution about what is a fast-developing technology is sensible, wood’s proponents have pointed out that no material is perfect: steel buckles, concrete cracks, wood burns.
Fire resistance can be enhanced through encapsulating combustible materials in non-combustible materials such as plasterboard and cavity barriers, notes Tadman.
The European design codes for timber structures are currently being revised too, which will result in even safer buildings, believes Abrahamsen of Moelven Limtre, the glulam company.
The 20th century was the century of concrete. The 21st century will be the time for timber
And that’s the crux, the knot in the wood: timber is likely to be the future. But it still needs protecting both from an environmental perspective and a construction one.
The central pillar of the Hōryū-ji Temple pagoda was made from a single Hinoki (Japanese cypress), felled in 594 AD. It has survived lightning strikes and a 7.2 magnitude earthquake.
The great Toryo, Tsunekazu Nishioka, believed that because of its painstaking 1934 restoration, the Hōryū-ji Temple will now stand for at least another 2,000 years.
“Hinoki has its own Hinoki’s life,” he wrote in his book Ki no kokoro, Tree Minds. “The life is longer than iron’s and concrete’s.”
Main image: Denmark’s Camp Adventure Tower spirals out of the forests near Copenhagen. Credit: Rasmus Hjortshøj